Biosolids and Energy Recovery Facility
2-minute video version - click here
IRWD’s Biosolids and Energy Recovery Facility is a state-of-the-art system that adds a second layer to the sewage treatment process. It converts the solids left over from the water recycling process into a valuable resource that can be used as fertilizer or fuel.
But we don’t stop there. The facility also harnesses the biogas produced from the process and uses it to generate electricity to power the facility.
The process begins when sludge from the adjacent Michelson Water Recycling Plant is pumped to the biosolids plant. The sludge is screened and then thickened by centrifuges to separate water from the solids.
From there, the thickened sludge is sent to a two-phase digester system. (The separated water is piped back to the Michelson plant, so no water is wasted.) Methane gas produced during the digestion process is used as fuel for the pellet drum dryer, and for micro-turbines to produce energy. The heat produced by the gas combustion is captured and used for heating the digestion process and some portions of the buildings.
The project reflects Irvine Ranch Water District’s commitment to sustainability, making good use of all byproducts from the recycled water process.
It also aligns with green and sustainable business practices, establishing cost-effective management of sewage services for IRWD customers.
The facility, which began operating in 2020, is next to IRWD’s Michelson Water Recycling Plant at 3512 Michelson Drive, Irvine. It is part of a larger land area that encompasses about 452 acres and includes the San Joaquin Marsh and Wildlife Sanctuary.
For more information, please email info@IRWD.com or call 949-453-5500.
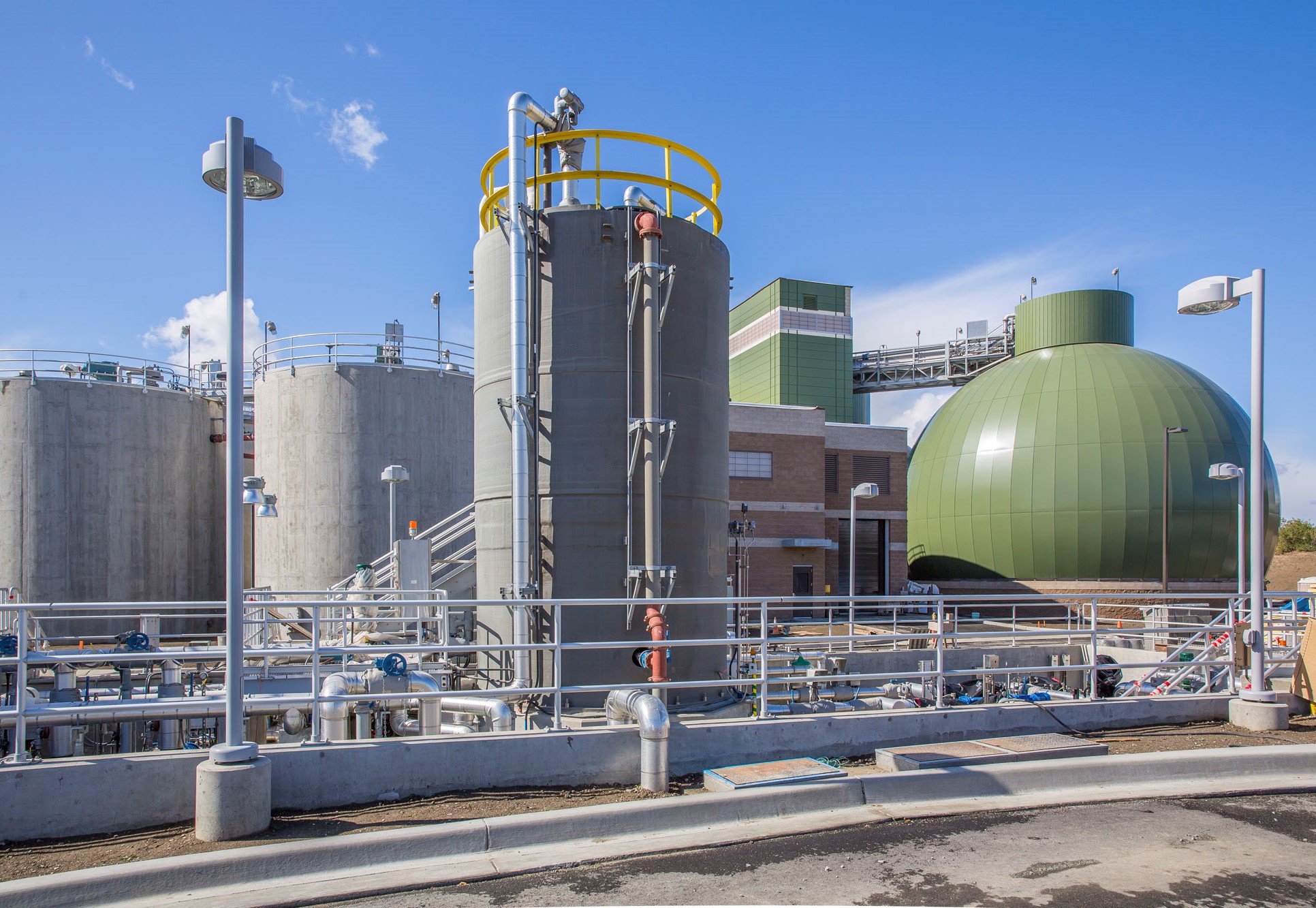
|
Biosolids are a nutrient-rich natural byproduct of the recycled water process, which treats the water in sewage for use in landscape irrigation and other uses. The residual organic solids are treated and converted into fertilizer or fuel.
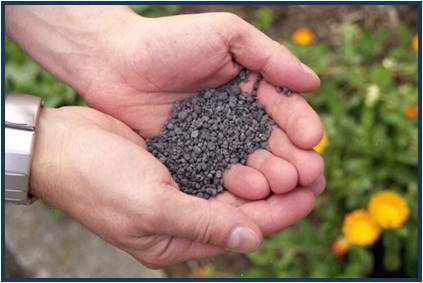
|